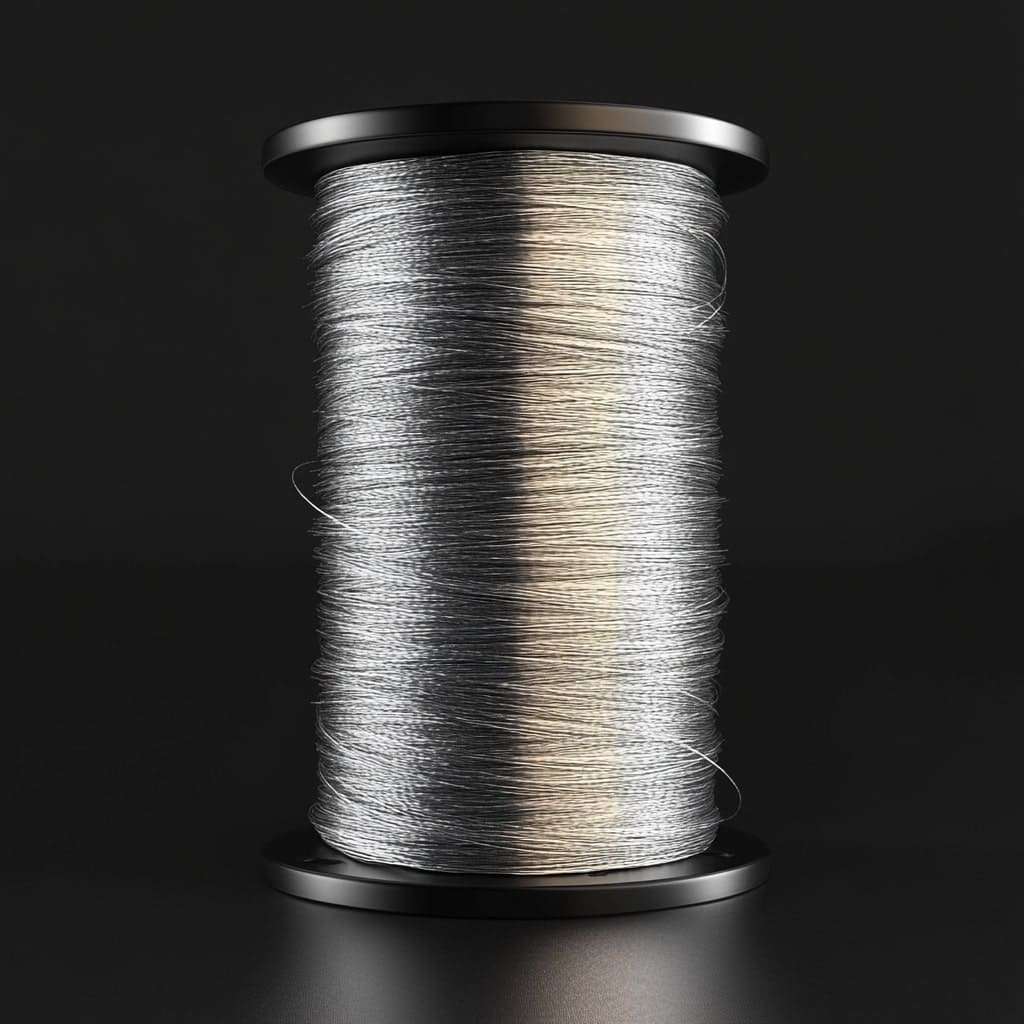
Nickel Microwires
High-Purity Nickel Microwire NP2 / NP1 (3N – 4N Purity Grade)
Available in diameters of 10 µm and 25 µm (micron). Each wire is precision-wound on sealed spools, with a net weight of 100–350 grams per unit, ensuring safe handling, protection from contamination, and seamless integration into advanced manufacturing workflows.
Product Gallery
Product Details
Real FAQs
Yes, trial orders are available for most products, excluding custom-engineered alloys. Please select the “Trial quantity required” option when submitting your RFQ form.
Yes, every delivery includes a lab certificate to verify product purity and ensure batch-to-batch consistency.
Yes, we assist with all necessary documentation to help streamline logistics, compliance, and customs clearance — regardless of the products combination or technical specifications in your order.
Other Products
High-Purity Nickel Microwire NP1 / NP2: Material Profile
Nickel Microwire NP1 / NP2 is a high-precision metallic conductor produced from non-alloyed nickel with controlled purity and dimensional tolerance. As a transition metal with a partially filled d-electron shell, nickel exhibits versatile oxidation states (commonly Ni²⁺), along with excellent mechanical strength and magnetic properties. Its melting point is 1455 °C, with a boiling point of 2913 °C, and it remains structurally stable under elevated temperatures and in reactive environments.
What distinguishes Nickel Microwire NP1 / NP2 is its extremely small diameter — typically 10 µm or 25 µm — paired with a tightly controlled surface finish, electrical conductivity, and ductility. These microwires are engineered for demanding applications in sensors, micro-coils, precision actuators, and microelectromechanical systems (MEMS), where minimal size and maximum performance are essential. The material’s high nickel content and purity ensure long-term stability under vacuum, thermal cycling, and electromagnetic exposure.
The performance of Nickel Microwire NP1 / NP2 is highly sensitive to trace contaminants and microstructural defects. Even low levels of sulfur, phosphorus, or oxygen can impair conductivity and long-term oxidation resistance. Therefore, strict metallurgical control is applied during manufacturing to ensure consistency in chemical composition, grain structure, and surface integrity. This is particularly critical in high-reliability systems such as aerospace electronics, medical diagnostics, and quantum-scale devices.
Product Form and Handling
Nickel Microwire NP1 / NP2 is supplied as ultrathin wire wound on sealed polymer or antistatic spools, each unit containing a net weight of 100–350 grams. The wire is uniformly wound to prevent tangling, mechanical strain, or contamination during storage and handling. Packaging is designed to maintain product integrity by protecting the wire from ambient moisture, airborne particles, and static charge.
Unlike bulk nickel forms, Nickel Microwire NP1 / NP2 requires precision handling during integration into manufacturing workflows. Its minimal diameter allows for tight winding, high-density assembly, and microscale interconnects, making it ideal for use in additive manufacturing, RF and biomedical coils, high-frequency sensors, and miniature instrumentation. In laboratory or cleanroom environments, the wire can be handled with vacuum tweezers or anti-static tools to avoid surface damage and maintain full functional performance.
Applications of High-Purity Nickel Microwires (NP1 & NP2)
Nickel microwires with diameters as fine as 10 μm and 25 μm offer a unique combination of electrical conductivity, corrosion resistance, mechanical strength, and thermal stability. The NP1 and NP2 series are engineered for ultra-sensitive and high-reliability environments across multiple industries: